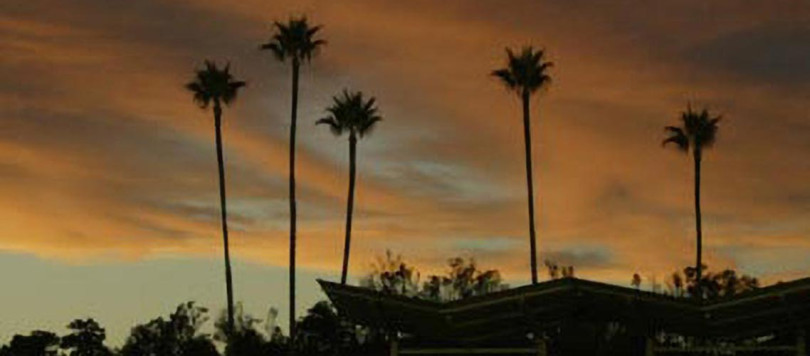
Feature
Comprehensive History
By Mark Langill
Stadium at Sunset
When the sun sets at Dodger Stadium, I am impressed first of all with the mountains because, at this time of year, they are fully defined. It makes me think of some of the great artists who did Western paintings — Frederic Remington, Charles Russell, Frank McCarthy, to name a few — because they must have been inspired by that.
And then the cloud formations. At sunset, they turn pink. And as it continues, the closer you are to sunset, the clouds are still kind of gold. Farther away in center field and right field, you’re away from the sunset and the clouds are turning purple. So you think of an artist’s palette with various colors, and it just takes your breath away.
Down on the field, a ballgame is just beginning. But the sunset becomes a major distraction because it’s so overwhelming it’s hard to take your eyes off it. And then the palm trees — there’s a group of palm trees on the hill behind left field — they are defined against the sky, and they are turning colors with the sunset. You can’t see that anywhere else in a ballpark.
Vin Scully
Los Angeles Times, August 21, 2003
Introduction
The dream of a grand baseball stadium materialized amidst the frustration, inspiration and determination of Walter O’Malley, whose creation of Dodger Stadium would become the crown jewel in a four-decade career in the major leagues.
It was the first privately-financed baseball venue since Yankee Stadium in 1923 and its fundamental amenities were designed for the fan, including a revolutionary concept of multi-level parking lots and an unobstructed view from any of the 56,000 seats. The Dodgers have the highest cumulative fan attendance in MLB history. Those millions of fans who have visited the ballpark since it opened in 1962 reflect how the home of the Dodgers became woven into the fabric of everyday life for the residents of Los Angeles and its surrounding communities.
While the faces wearing Dodger uniforms may change with the passage of time, generations have shared the breathtaking images of the 300-acre facility, nestled within the surrounding hills.
Envisioning a Ballpark
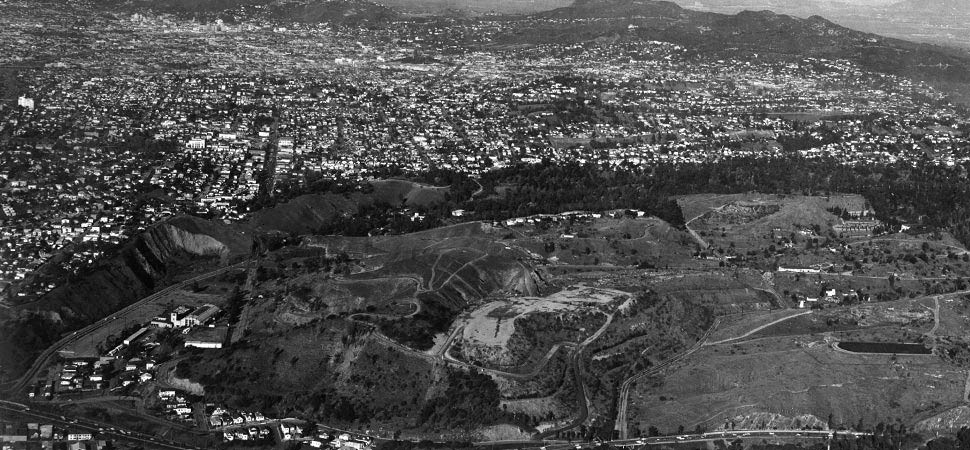
An aerial view of the land prior to the construction of Dodger Stadium.
Chavez Ravine was a difficult site because of a network of washes, gullies and gulches that were interlaced with hills and twisting roads. Elevations in the ravine ranged from 400 feet to 700 feet above sea level.
In order to compensate for this rough terrain, more than 8 million cubic yards of earth was moved to reshape the area. The steeply terraced bowl of the towering hillside site became an integral part of the main grandstand structure and located the stands on a slope in the shelter of the U-shaped hill.
Next, the Northern face of the rock and sandstone hill was cut down and shaped into a rough amphitheater and benches were cut into the sloping floor to support the stadium foundations and pedestals. To control erosion, a two inch-thick concrete was sprayed over the area. The 124-foot-high grandstand has three major cantilever tiers built on 78 precast bents.
“It’s still the most beautiful ballpark in the major leagues,” said Dodger Hall of Fame broadcaster Vin Scully said. “Over the years, the backdrop beyond the outfield has increased in beauty and the landscape is so inspiring, especially at twilight on those cool summer evenings. There isn’t anything to distract a baseball fan when coming to a game at Dodger Stadium. The ballpark is surrounded by beauty and everyone can focus on the game. Even fortysomething years after it was built, the stadium is a tribute to Walter O’Malley’s vision.”
When the Dodgers moved from Brooklyn to Los Angeles in 1958, there were many suggestions about the design of the new ballpark. O’Malley left New York after an exhaustive 10-year campaign to replace Ebbets Field, a cozy but aging facility in the middle of a Flatbush neighborhood which had a 32,000-seat capacity and parking for 700 cars.
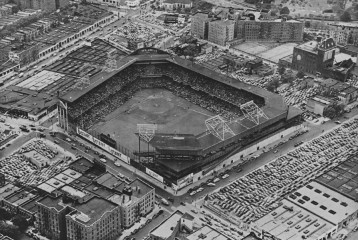
The cozy confines of Brooklyn’s Ebbets Field left little room for parking or expansion when the Dodgers began a search for a new ballpark following World War II.
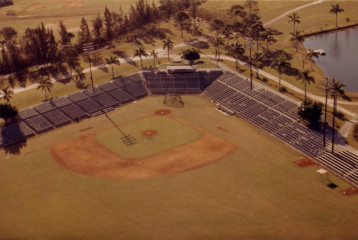
Holman Stadium in Vero Beach, FL opened in 1953 and was designed by Captain Emil Praeger, who also was the architect for Dodger Stadium construction.
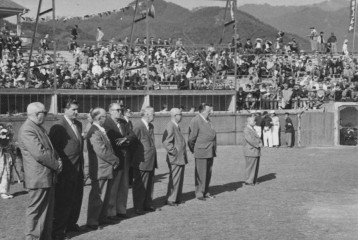
The “dugout boxes” at Japan’s Korakuen Stadium, where the Dodgers played many exhibition games during their 1956 goodwill tour, would be incorporated into the design of Dodger Stadium.
As the Dodgers’ legal counsel, O’Malley penned a letter on Oct. 14, 1946 to Emil Praeger, a distinguished Navy captain who developed the original design of the concrete floating breakwater during World War II. Praeger, who was in charge of all engineering projects for the Department of Parks in New York City, also played major roles designing the renovation of the White House and the Los Angeles Public Library.
Of a potential new ballpark in Brooklyn, O’Malley wrote: “They say everything happens in Brooklyn, but here is something that didn’t. Your fertile imagination should have some ideas about enlarging or replacing our current stadium …” O’Malley letter to Capt. Emil Praeger, October 14, 1946
Praeger didn’t get a chance to build a ballpark in Brooklyn, but O’Malley received a sneak preview of Praeger’s capacity when the two teamed to build a 5,000-seat facility at the Dodgers’ spring training headquarters in Vero Beach, FL. Holman Stadium, which opened in 1953 and remains the centerpiece of the modern-day Jackie Robinson Training Complex, was the first major improvement on the Dodgertown property, a former naval air station.
During his negotiations with New York officials, O’Malley also met with Los Angeles representatives after the 1956 World Series. On a May 2, 1957 helicopter tour, O’Malley was shown the land where he immediately envisioned freeway access from all directions. The Dodgers traveled to Japan following the 1956 World Series. O’Malley was inspired by the ground-level seats at Korakuen Stadium and would incorporate “Dugout” seats in his Dodger Stadium plans.
Exchange of Land
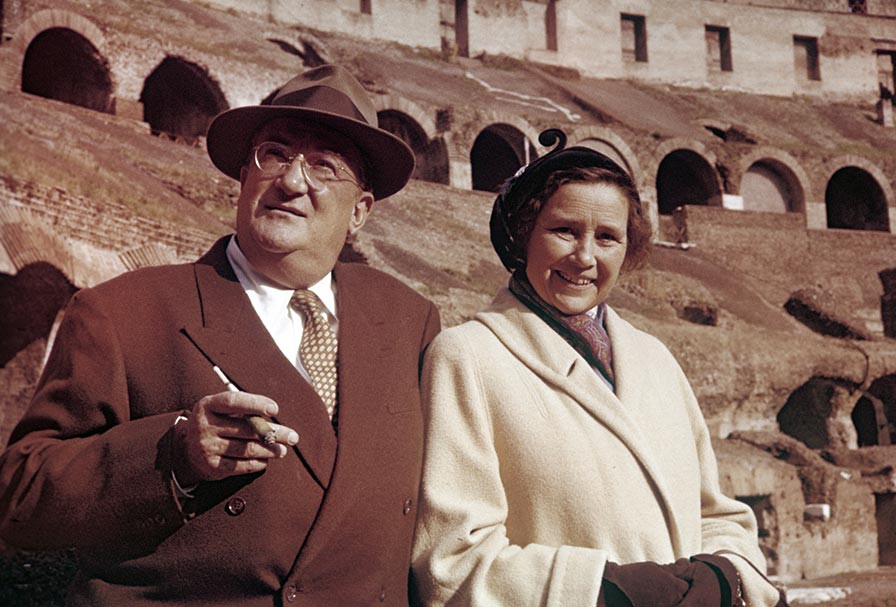
Walter and Kay O’Malley observe the famed Roman Colosseum as part of their around-the-world family trip following the Dodgers’ goodwill tour to Japan in 1956.
After the Japan tour, O’Malley made a side trip to Italy before returning to the United States. O’Malley studied the Colosseum in Rome, which took 12 years to build and was completed in 82 A.D. The Colosseum seated an estimated 50,000 to 80,000 and remained the largest “stadium” until the Yale Bowl at New Haven was built for football in 1914 to accommodate 80,000 spectators.
While O’Malley examined his remaining options in New York, he pondered the landscape in Los Angeles. In a letter to Dodger stockholder James Mulvey on Jan. 8, 1957, O’Malley described a Thomas Brothers map book of Los Angeles County and the areas of Elysian Park and Chavez Ravine.
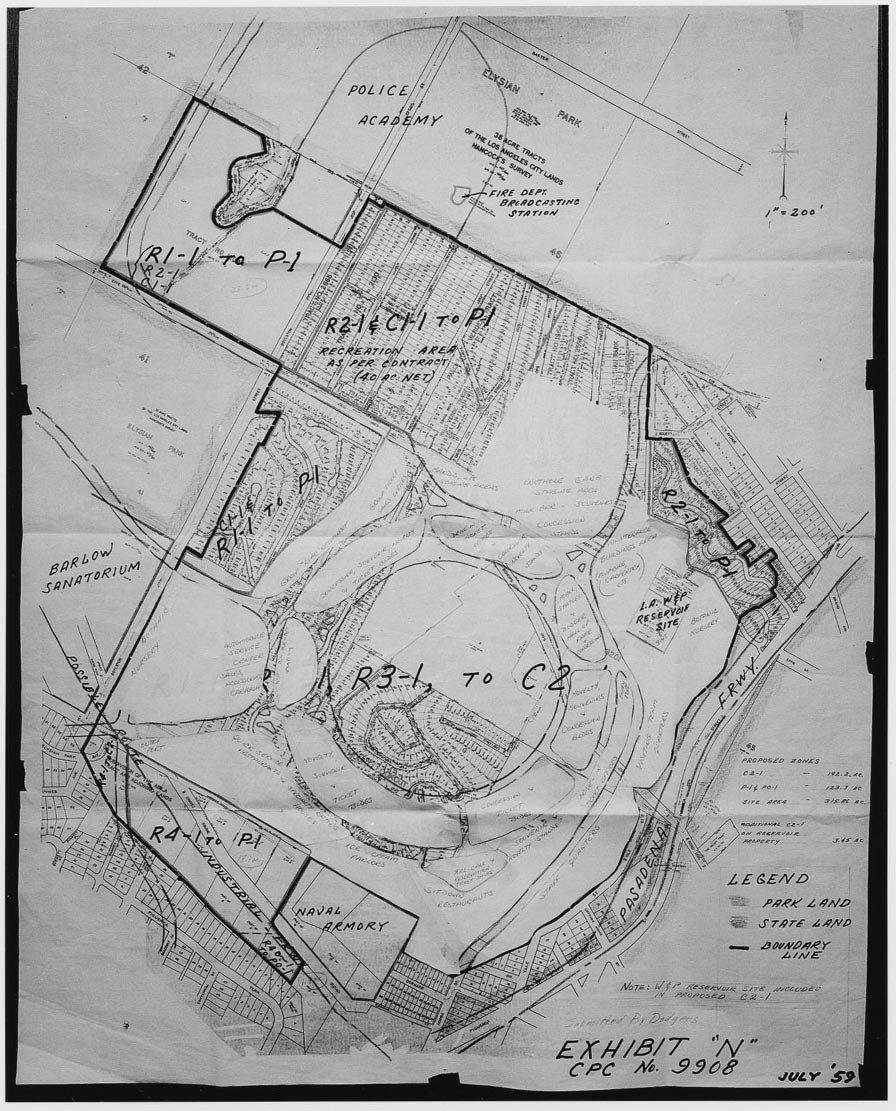
This map of Los Angeles and the hilly area known as Chavez Ravine would provide the setting for the construction of Dodger Stadium.
“On page 44 of the booklet just to the right of the center on the top you will find Chavez Ravine Road,” wrote O’Malley. “This particular map shows the freeways more clearly. There are about 400 acres of sandy hills and underdeveloped land in this area behind the Police Barracks. … I wish you would drive out to this location at your convenience and study it. This happens to be the only spot adjacent to one freeway but within a short distance of the intersections of the remaining highway. … When you return to New York, we will have some interesting observations to compare …” O’Malley letter to James Mulvey, January 8, 1957
In February 1957, O’Malley purchased the Chicago Cubs’ minor league franchise, the Los Angeles Angels, along with their home ballpark, Wrigley Field. O’Malley secured the territorial rights to the Los Angeles market and had a home if the team was unsuccessful building a new stadium in Brooklyn.
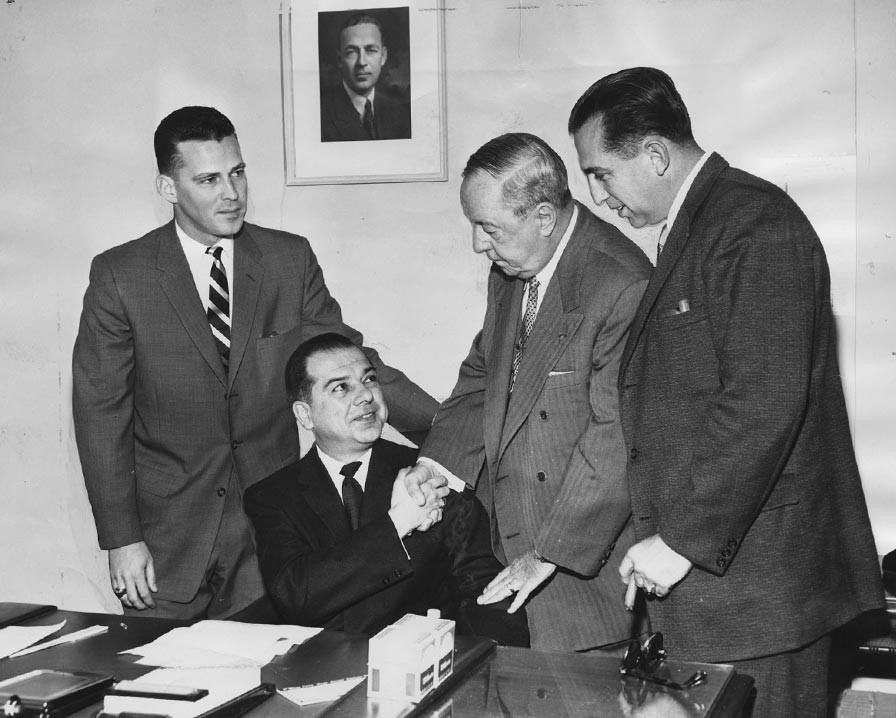
The exchange of the Dodgers’ minor league Ft. Worth (TX) club to the Chicago Cubs for the Pacific Coast League’s Los Angeles Angels and Wrigley Field ballpark on Feb. 21, 1957 was one factor in later opening the door to the West Coast for the Dodgers. Chicago Cubs owner Philip K. Wrigley was a supporter of major league expansion. From left, Dodger Vice President Dick Walsh, Angels Business Manager Bill Heymans, Cubs Vice President Clarence Rowland and Dodger scout Harold “Lefty” Phillips.
Copyright © Los Angeles Dodgers, Inc.
Negotiations with New York City officials eventually fizzled and Los Angeles agreed in September to exchange 300 acres of land in Chavez Ravine to the Dodgers in return for the Dodgers’ commitment to build a 50,000-seat stadium. The Dodgers also exchanged the deed to Wrigley Field to the city and agreed to pay a property tax estimated at $345,000. The contract also included a commitment from the city to spend $2 million on grading for the area and $2.74 million from the county for the construction of access roads.
Facing Legal Challenges
The contract would trigger legal challenges and a public referendum while the 1958 Dodgers played their first season on the West Coast at the Los Angeles Memorial Coliseum, a venue designed for football and track. At the height of the referendum debate, Los Angeles Examiner columnist Vincent X. Flaherty answered his own hypothetical question about the Dodgers’ commitment to staying in Los Angeles.
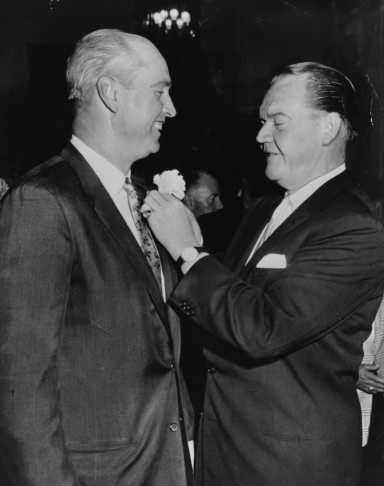
Los Angeles Examiner columnist Vincent X. Flaherty pins a flower on Dodger Manager Walter Alston at a “Welcome Dodgers” luncheon prior to the 1958 season opener. Flaherty initially corresponded with Walter O’Malley in 1953, expressing the interest of Los Angeles officials to bring Major League Baseball to the West Coast.
AP Photo
“Best way to keep the Dodgers here is to let them spend from $12 million to $15 million improving the now desolate property,” Flaherty wrote. “It will take them 22 years to pay off the debt.”
O’Malley wanted to build his ballpark without being a tenant in a municipal stadium. Others couldn’t imagine a bigger picture when O’Malley, as a member of baseball’s executive council, made a prediction in 1953 when discussing the Supreme Court’s decision to uphold the “reserve clause” in baseball contracts.
“I am pleased that the integrity of baseball has been reaffirmed by the Supreme Court,” he said. “But the decision does not mean that baseball will go along with the horse and buggy days. We must clearly recognize the changing conditions and particularly the possibility of territorial expansion.” Current Biography, March 1954 issue
There were no ballparks built during the 1940s and when the National League Braves moved from Boston to Milwaukee in March 1953 it was the first franchise shift in 50 years. Attendance records in Milwaukee and the emergence of the Braves as a pennant contender in the mid-1950s added pressure to O’Malley in his quest for a new ballpark.
Actor Joe E. Brown, the master of ceremonies at the Dodgers’ Opening Day 1958 festivities at the Los Angeles Coliseum, served as the general chairman of the Taxpayers Committee for Yes on Baseball, the baseball referendum measure approved by Los Angeles voters on June 3, 1958.
“A great advantage of the contract between the city and the Dodgers is that the city will exercise continuing control over Dodger plans for development of Chavez Ravine,” Brown said. Los Angeles Times, May 26, 1958
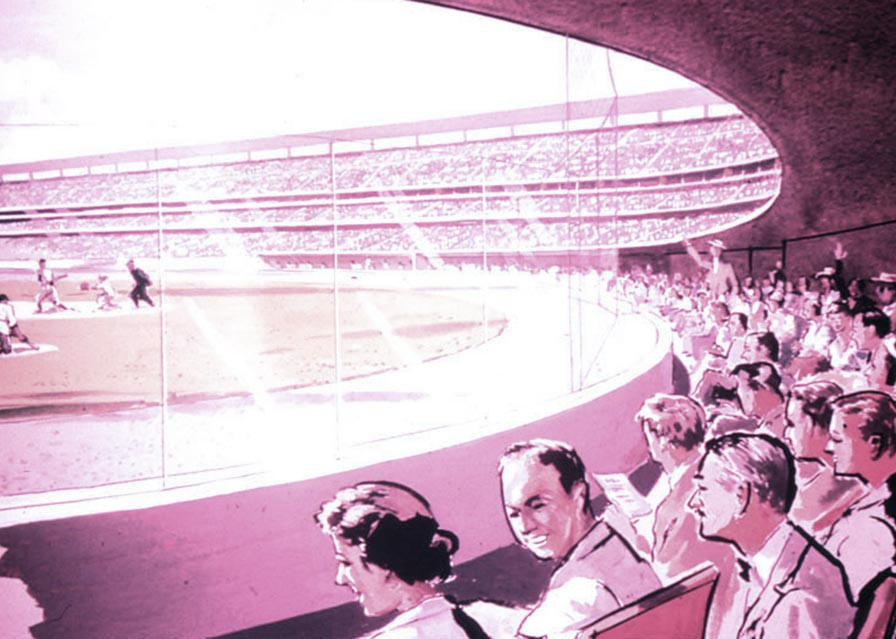
An artist’s sketch of the new Dodger Stadium dugout seats, which were inspired by the similar design of the dugout seats at Korakuen Stadium in Tokyo, Japan.
Among the early ideas from architects were special bus lanes for public transportation, a nursery for preschool-age children; a 40-acre public recreation center and a “sky terrace restaurant on the highest tier.” The Dodgers also contemplated bypassing the conventional wire screen behind home plate along the first and third base lines with plexiglass to improve visibility.
O’Malley’s original map submitted in 1959 to the City Council included what the Los Angeles Mirror described as “a myriad of commercial enterprises; auto service center, novelty and souvenir shops, restaurants, car wash centers.” The blueprints also proposed a Dodger Hall of Fame, botanic garden, a mall, drive-in ticket offices and quarters for both staff and visiting teams.
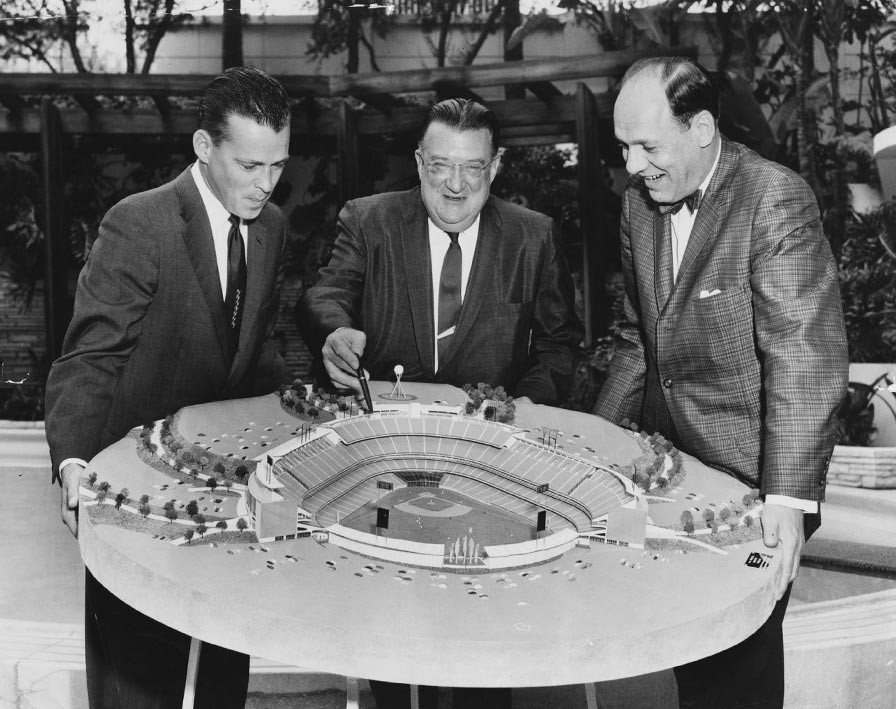
Walter O’Malley inspects a model of Dodger Stadium with Vice President, Director of Stadium Operations Dick Walsh (left) and Executive Vice President and General Manager E.J. “Buzzie” Bavasi.
Copyright © Los Angeles Dodgers, Inc.
The Drawing Board
Other ideas in the subsequent months included a tram service from the distant areas of the terraced parking lots, and a “secret” that was revealed in 1960 when Hollywood producer Mervyn LeRoy commissioned a scale model of Dodger Stadium to acquaint the fans with the conveniences, comforts and beauty of their new stadium. The model was displayed at the Bank of America building on South Spring Street.
“Now that the model is about to go on display, one of the secrets of the Dodgers had hoped for their first night game will be out,” a team press release said. “Here it is: Whenever a Dodger hits a home run in the new stadium, vari-colored spotlights will play on the cascading waters of a picturesque fountain in center field. No fireworks. The fans can make the noise.”
The fountain remained on the drawing board, but the behind-the-scenes planning and brainstorming sessions with professional architects, co-workers in the Dodger front office and general baseball fans affirmed O’Malley’s personal challenge to make the ballpark a special destination among an already large list of Southern California attractions, landmarks and amusement parks.
“Don’t ever doubt that Walter is a showman,” Dodger Vice President Dick Walsh told the Los Angeles Times in October 1960. “Walter knows that baseball today demands more than three outfield walls and a covered stand. Chavez Ravine will have every innovation known to baseball — and a few known only to Walter.” Los Angeles Times, October 3, 1960
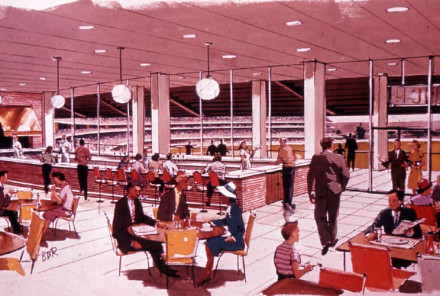
An artist’s rendering of the fine dining available for patrons of the new Stadium Club restaurant located on the Club Level at Dodger Stadium.
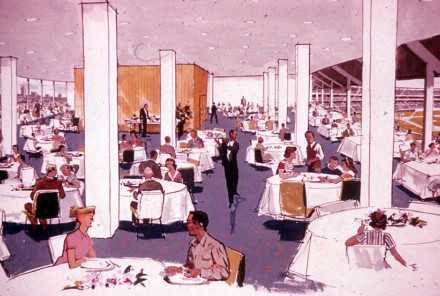
Members of the Stadium Club could watch the ballgame from either their box on the Club Level or within the confines of the elegant restaurant.
And there were plenty of ideas swirling in O’Malley’s mind. He jotted notes in 1958 with questions, observations and plans about everything from locker room blueprints to the menus at the various concession stands. The following categories are from O’Malley’s personal files:
Tram — World Fair type of transportation 25-cent charge from car to seats. Stations, turnstiles, pipe railing. Also use as guided tour before and after games and when team is away. Loud speaker like Disneyland with mike for driver. Tricky cars and locomotion, perhaps to pass through tunnels, a Hall of Fame, etc. Designed to attract youngsters.
Location of restaurants — Perhaps they could be worked in like at Roosevelt Racetrack in New York to have picture window of playing field and levels for tables could be terraced. Closed circuit TV set should be in restaurants and near concession stands.
Seats — 52,000 minimum with 2 step enlargement provision to 60,000 and 70,000 (to be largest BB park.)
Controlled air drafts — Prevailing wind is from the West (check exact compass direction). How to control this and get it to the stands and playing field — by movable louvered design? Do not want this to be a hot box. April, May and June evenings are a cool 60 degrees. Should we take the edge off this by radiant directed heat (infra red)?
Outdoor Cathedral of trees — like McKee Jungle Garden in Vero Beach planting of Royal Palms, or metasequoia, a restful landscaped place, fountains, benches, water, fish, peacocks, ducks, etc.
Fountains — With colored light. This seems to be an economic way to get architectural effects and to add to beauty. Lake and streams. The different elevations lend themselves to a recirculating system. See Hollywood Racetrack. We want this PARK to be a public attraction even when no events are scheduled.
Monumental effect — As this stadium will be largely buried in the ground, we might need something vertical and impressive. Perhaps an elevated water tower in the shape of a baseball with flood lights. Change color as home team leads or trails. This site when in use at night can be seen from most of the outlining districts, Hollywood, Beverly Hills, etc. Trylon and perisphere World Fair idea? Baseball and crossed bats in a tripod?
Unveiling Plans
The Dodgers couldn’t reveal all their plans, but the following text was contained in a 1959 scorecard message to the fans under a sketch of a multi-level backdrop to a batter swinging at home plate:
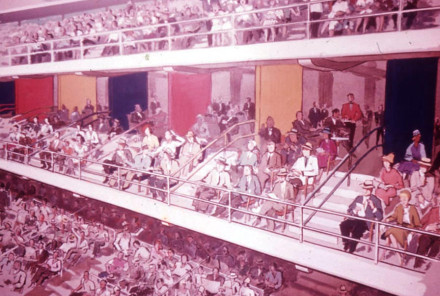
An artist’s sketch of the multi-colored Club Level seating, located between the Loge and Reserved Levels at Dodger Stadium.
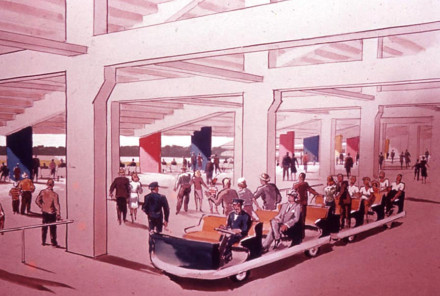
Early concepts of the new Dodger Stadium included ways to shuttle fans from the parking lots to their seats.
“Your Dodgers’ Home of Tomorrow … Artist’s conception of an inside-the-park view of the stands as they will be for the new Dodger Stadium in Chavez Ravine. In this “dream about to become a reality” Dodger fans will be afforded the finest seating arrangement in any outdoor arena, unobstructed vision from every seat, terraced parking which will enable fans to drive to their section in the stands with practically no walking or climbing, restraints for all, a Stadium Club for season boxholders, unmatched beauties in landscaping, numerous lanes for rapid departure of cars and buses after the games, the most modern lighting equipment in baseball for night ball, a field of balanced playing measurements in left and right field, a breath-taking, sky-high view of the amazingly picturesque Los Angeles area and many other features which will make this new Stadium a landmark of world-wide acclaim. On June 3, 1959, anniversary of the Referendum vote of 1958 in which the Los Angeles citizens approved the transfer of Chavez Ravine to the Dodgers, the contract was signed by the City and Dodgers. The ballclub will now strive to meet its target date — Opening Day, 1960.”
Further delays by opponents of the project delayed the actual construction of the stadium until after Labor Day 1960, which left only 19 months to move the remaining 5 1/2 million yards of dirt en route to building the stadium.
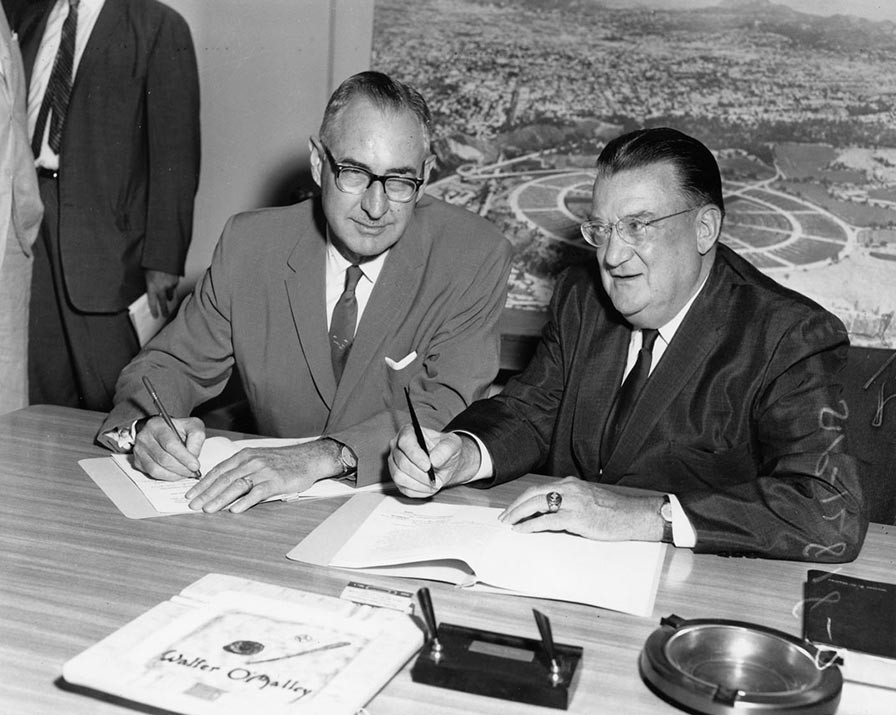
A.S. “Al” Vinnell signs the contracts to begin the construction of Dodger Stadium on Aug. 25, 1960.
Courtesy of University of Southern California, on behalf of the USC Specialized Libraries and Archival Collections
On Sept. 3, 1959, a $646,890 contract for grading the site of Dodger Stadium was awarded by the Board of Public Works to Vinnell Constructors of Alhambra, which submitted the lowest bid among 11 submitted in July and was 9.8% under the city’s estimate.
Jack Yount, the Vinnell contractor in charge who specialized in concrete projects and had experience with freeway interchanges in Southern California, never imagined his company would be asked to build the ballpark using Praeger’s designs and O’Malley’s input. Yount originally wanted only to bid on the leveling of the land. The specialty of the company was installing the sewers and drainage areas associated with any municipal project involving large amounts of concrete.
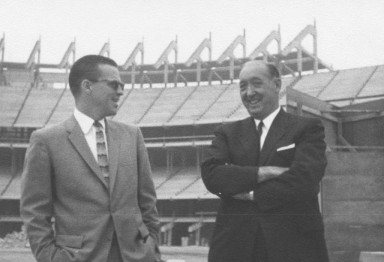
Dodger Vice President Dick Walsh shares a laugh with Jack Yount, the Vinnell Constructors partner in charge of the Dodger Stadium construction project.
In a 1971 interview, Yount recalled Praeger wanted Yount to personally supervise the building of the ballpark and feared a deal with another company might lead to delays with subcontractors. O’Malley also wanted Dodger Stadium to be made of concrete instead of steel.
On August 25, 1960, O’Malley signed a contract with Vinnell for the entire construction of the 56,000-seat stadium. The formal signing at the Dodger office in the Statler Hotel at 930 Wilshire Blvd. in downtown Los Angeles cleared the final hurdle for the building of the stadium, although O’Malley said all the refinements might not be ready for Opening Day 1962.
Once the earthwork was well under way, the contractor started to cast and erect the 23,000 concrete members in the grandstands. The consulting engineers planned a casting yard on the job because there was available space and some of the members, especially the 32-ton frames, were too large to truck into the site.
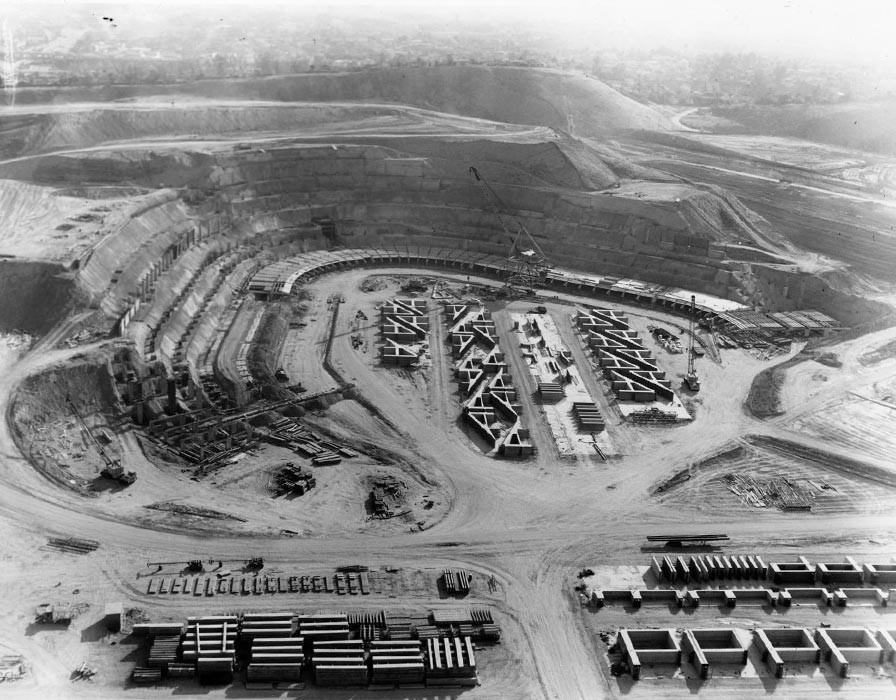
A six-acre casting yard and special one-time use $150,000 crane were crucial to the rapid 19-month construction of Dodger Stadium.
Concrete Ideas
Vinnell built a six-acre casting yard. The concrete casting beds were 3 inches thick, 50 feet wide and between 200 and 400 feet long. Vinnell cast the 22-foot-long seat units in steel side forms and cured them with steam. All other concrete members were cast in wood forms and covered with curing compound.
There were more than 25,000 separate pieces, all cast before the construction began. Each piece of concrete was marked and catalogued so the erection crew could find it. Yount also utilized fiberglass molds instead of steel. The pieces were cast on the property and a special $150,000 one-time use crane was assembled at the stadium site to move the pieces in place.
“There is a lot more strength in this stadium than there is in highway bridges,” Yount said. “On this structure, we used almost seven sacks of cement a yard. On freeway bridges, they use five. For paving, they use four or less. So every yard of concrete poured at the stadium cost O’Malley about $1.50 extra just in cement alone. There are about 45,000 yards in the whole stadium.”
As the stadium began to take shape, O’Malley announced the stadium would have 52,000 seats and could be expanded in stages to boost the capacity to 67,000 and eventually 80,000. O’Malley made it clear expansion might not be necessary.
“It naturally depends on business,” he said. “Remember, when you expand your seating, you must expand your paved parking area, too. Before we take on these expenses, we must be assured there is sufficient demand.” He later settled on a 56,000-seat capacity.
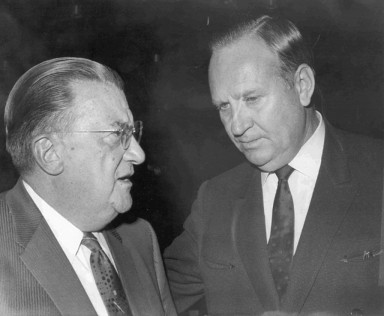
Walter O’Malley and Los Angeles Angels Owner Gene Autry discuss a compromise that had been reached to allow the new American League team to play in Los Angeles in 1961. The Dec. 8, 1960 owners’ meeting was held in St. Louis.
AP Photo
And O’Malley gained his first tenant during construction when the expansion Los Angeles Angels joined the American League in 1961. The Angels, owned by motion picture star and radio executive Gene Autry, would play their inaugural season at Wrigley Field and move into the new ballpark in 1962.
On Nov. 22, 1961, the first of 47,964 seats were fixed into place by representatives of the American Seating Company of Grand Rapids, MI. The amount was one of the largest single stadium installations in history. If placed side by side, the seats would form a row nearly 33 miles long. The seats required 350,000 feet of board lumber, 546 tons of cast iron and 3 tons of aluminum nuts and bolts.
Another challenge arrived in the form of torrential rains that hit Southern California early in 1962 and threatened the project’s target date for Opening Day. The field was graded and ready for sod when the first rains came in February. It took 10 days to dry out and reconditioning for the field to be graded again and 150 square feet of sod was installed before another five-day series of storms washed away the top soil, causing an estimated $500,000 in damages.
Visit to Disneyland
There were reports the Dodgers would have to relocate the 1962 opening series to Cincinnati’s Crosley Field and Milwaukee’s County Stadium. The Angels, scheduled to open their season on April 17, had until April 1 to exercise an option to return to again use the 22,000-seat Wrigley Field, which would also be available to the Dodgers in case of emergency.
“I wouldn’t even consider anything other than Chavez Ravine for April 10 and every date thereafter,” O’Malley said. “I’m a stubborn man. We will hit the target date, no matter what the weather. I have a competent engineer and a good contractor and they assured me within the last hour that we’ll open as scheduled in Chavez Ravine.” Herald-Examiner, February 11, 1962
The first 22 days of February 1962 produced 17 inches of rain and the waterlogged playing field required creative drying solutions. An Allison jet airplane engine from an F-84 fighter plane was mounted on a truck. Moved to various locations on the field, the engine spewed a jet blast of 300 feet of heat estimated at 250,000 BTU’s (British thermal units). Two helicopters were also employed to help dry out the field with their powerful downdrafts of air. The jet engine was also eyed for future use if needed to dry the access-road beds leading into the stadium so they could be blacktopped.
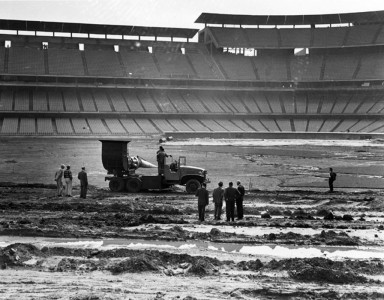
Heavy rains in February 1962 prompted creative methods of drying the playing surface at Dodger Stadium, including bringing an Allison jet airplane engine from an F-84 fighter plane mounted on a truck.
AP Photo
As the stadium began to take shape, sportswriters focused on the makeup of the 1962 ballclub, which included starters Sandy Koufax, Don Drysdale and Johnny Podres — all whom might benefit from a “pitcher’s park.” The regular lineup included potential power from Frank Howard, Tommy Davis and Duke Snider. The departure from the Coliseum would also change the fortunes of Wally Moon, the left-handed hitter whose opposite-field home runs over the screen were dubbed “Moon Shots.”
The field itself would be one of the few major league parks with symmetrical dimension — 330 feet down both left and right field foul lines; 380 feet to both left and right center; and 410 feet to dead center.
“If we blow the championship, I’ll take the rap,” O’Malley said. “Maybe right field is too deep for our particular personnel, but I’m a believer that dimensions should be synchronized, and not change from year to year.
“Blame me, if there’s any blame. It was my idea. I’ve always wanted symmetry in a ballpark and some day I’d like to see all the stadiums with identical dimensions. It would mean much more in the record books and in making comparisons.” Herald-Examiner, January 16, 1962
In Houston, meanwhile, team officials took a different approach to the field dimensions as the Colt .45s played in a ballpark noted for its tall infield grass. Said Manager Harry Craft: “When we make any changes in our park, it’ll be to suit ourselves, no one else.”
Dodger Stadium front office personnel visited Disneyland during the preseason, but not necessarily for a vacation. O’Malley wanted his employees to study the customer service at Walt Disney’s Magic Kingdom.
In his ballpark, O’Malley wanted to make sure his restrooms were clean, a vital element in the quest of family atmosphere and entertainment. There would be 48 restrooms throughout the park. At Wrigley Field, there were no second-tier restroom facilities.
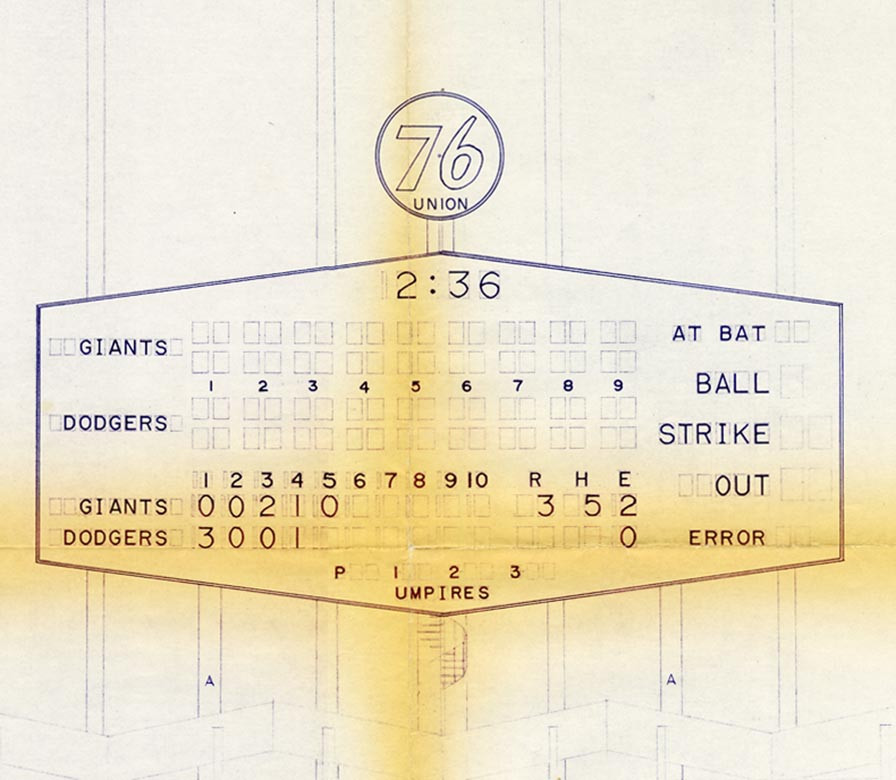
An artist’s rendering of the octagon-shaped scoreboard sponsored by Union 76 for Dodger Stadium’s opening.
World’s Largest Scoreboards
The scoreboards at Dodger Stadium were designed for baseball information and public announcements instead of the “bells and whistles” style of the famous “exploding scoreboard” at Bill Veeck’s Comiskey Park in Chicago.
The “world’s largest scoreboards,” which were 75 feet by 34, featured 17,000 lights, using enough electricity to light up 200 houses or 100,000 Christmas trees. The field scoreboard was installed by Olen Williams of the Fair Play Manufacturing Co. of Des Moines, IA, builder of the equipment. The left field message board was operated by Tom Seeberg, an assistant to Dodger publicity director Red Patterson. Seeberg sat at a machine modeled on a typewriter and could relay Patterson’s information using eight rows of words or numbers, each row having a space for 31 characters. By comparison, the Yankee Stadium scoreboard had eight rows with room for eight characters.
The Dodger Stadium messages could be delivered in four different ways: taped for eventual transmission; flashed instantaneously letter by letter; delayed line by line or delayed until completed and flashed in total.
O’Malley and Praeger also dreamed up a safety precaution pertaining to the outfield wall. Wary of Brooklyn’s Pete Reiser and others who were injured crashing into brick, concrete, hardwood or steel fences, the Dodger Stadium outfield walls were constructed with “tissue thin” plywood. There was also a cinder track inside the fence to warn an outfielder he was approaching the wall.
“If baseball is dying, as so many Cassandras have lamented, somebody forgot to tell Walter O’Malley,” wrote New York sports columnist Bob Considine. “The arena he has built with the cooperation of the City of Los Angeles is a temple, indeed a shrine, to the old game. No rich doting patron of the past, including (former Yankees owner) Jake Ruppert, ever made a contribution of such scope and imagination.” Bob Considine, Herald-Examiner, February 2, 1962
On March 29, O’Malley sent the following Western Union telegram to Praeger and John Waterbury in New York: “WOULD LIKE WALL BEHIND DUGOUT BOX SEATS RUNNING FROM ONE DUGOUT TO OTHER TO BE PAINTED IN THE RAINBOW SPECTRUM.” Overall, the ballpark’s color scheme features six different pastel shades.
The Dodger players who spent spring training in Florida finally had a chance to see the new ballpark on April 9, the day before the season opener with the Cincinnati Reds. A citizen’s committee sponsored a “Grand Opening” event for the Dodgers and Angels.
“This is a thrilling day for Los Angeles,” Baseball Commissioner Ford C. Frick said. “We should have nothing but praise for the man who imagined a city on the side of a hill and moved mountains to accomplish it — Walter O’Malley.”
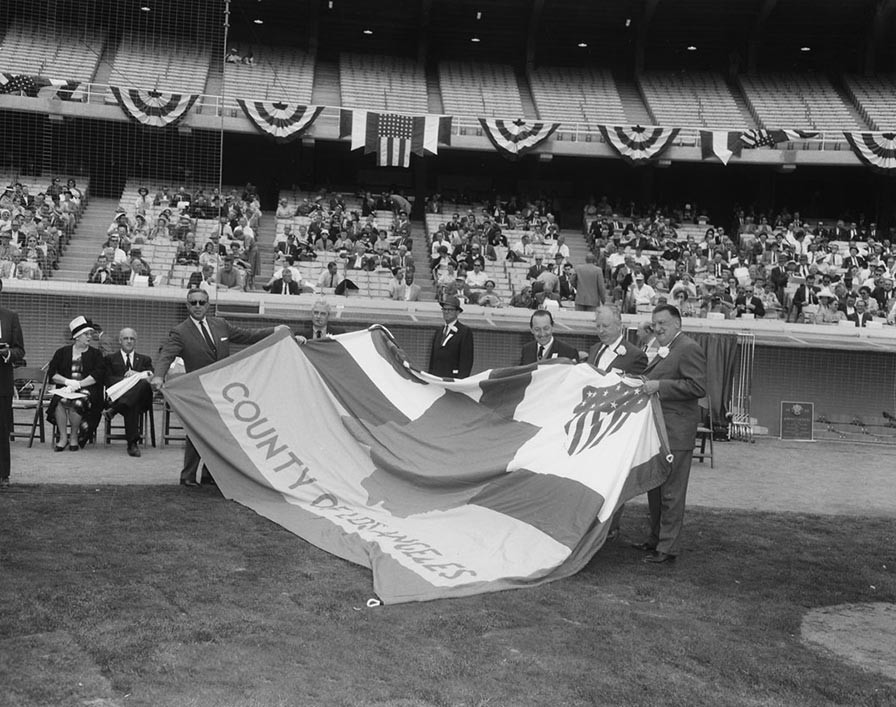
Preparations for pregame ceremonies at Dodger Stadium on Opening Day, April 10, 1962.
Opening Day Preparation
An estimated 2,000 fans attended the outdoor luncheon as civic leaders and baseball officials celebrated the end of the project — at least its frantic final hours as Teddy Buckner’s Dixieland band played alongside the sounds of Yount’s construction crews.
“When O’Malley, Frick and the rest of the dedication committee arrived at the stadium for the ceremonies, workmen were still scurrying around all four tiers, hammering, welding, plastering and painting,” Sports Illustrated reported. “A huge orange crane stood in left field lifting sections of the electronic message board into place. The grass, which had been grown outside the stadium and then carted inside in squares a few weeks before, was uneven and splotchy. Half of it had been dyed a rich green, but the other half was an unhealthy yellow. Delivery boys raced wildly about with bunches of flowers asking ushers where such-and-such a place was. The ushers could only shrug. Even the Dodgers’ batting cage got lost, preventing the team from taking batting practice.” Sports Illustrated, April 23, 1962
When a reporter noticed misspelled stadium signs (“Lounge” instead of “Loge”; “Pavillon” instead of “Pavilion”), O’Malley roared with laughter. Those typos were mere blips on the radar screen as the cranes were lifting the final pieces of the scoreboard in place and furniture was being moved into vacant spaces.
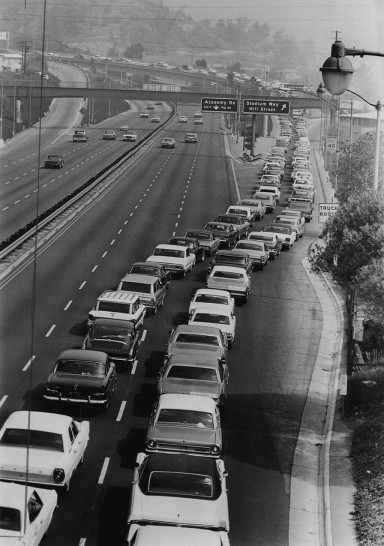
A steady stream of cars makes its way to Dodger Stadium, which would become a familiar sight during the next six decades.
Los Angeles Times Collection, UCLA Library Special Collections
“We’ll undoubtedly have a lot of glad moments in the new ballpark,” Snider said. “But we’ll probably have some sad ones, too.”
Snider suffered the season’s first injury on his way to the ceremonies. When the tailpipe on his car fell off in traffic, he picked up the loose piece of metal — not realizing it was still hot. Snider wore a golf glove over his hand to hide the burn during the ceremonies and keep himself in the next day’s starting lineup.
There were warnings about Opening Day traffic snarls and Los Angeles Police Chief William Parker urged fans to carpool and to arrive early after studying maps of new stadium access roads.
Dodger starting pitcher Johnny Podres took the advice and left his headquarters at the Mayfair Hotel at 8:55 a.m. The cab ride lasted just 10 minutes, leaving Podres plenty of time before the first pitch.
Alston nearly didn’t make the big event after waking up with a 100-plus temperature. When the Dodgers played their first game at the Coliseum in 1958, Giants Manager Bill Rigney was out of commission due to a sinus condition that prevented him from riding an airplane. Rigney was now the skipper of the Los Angeles Angels.
According to Los Angeles Times columnist John Hall, Moon hit the first home run in batting practice, “a 370-foot bolt into the right field bullpen.” Players who marveled at the beautiful grass during batting practice noticed the baseballs were turning green. At the suggestion of Mervyn LeRoy, the groundskeepers had sprayed the turf with a deep green dye the previous night.
Kay O’Malley, wife of the Dodger President, threw out the ceremonial first pitch. Also honored was Mrs. James (Dearie) Mulvey, Dodger stockholder who traveled from her New York home to visit Los Angeles. Mrs. Mulvey had also witnessed the Dodgers’ first game at Brooklyn’s Ebbets Field in 1913.
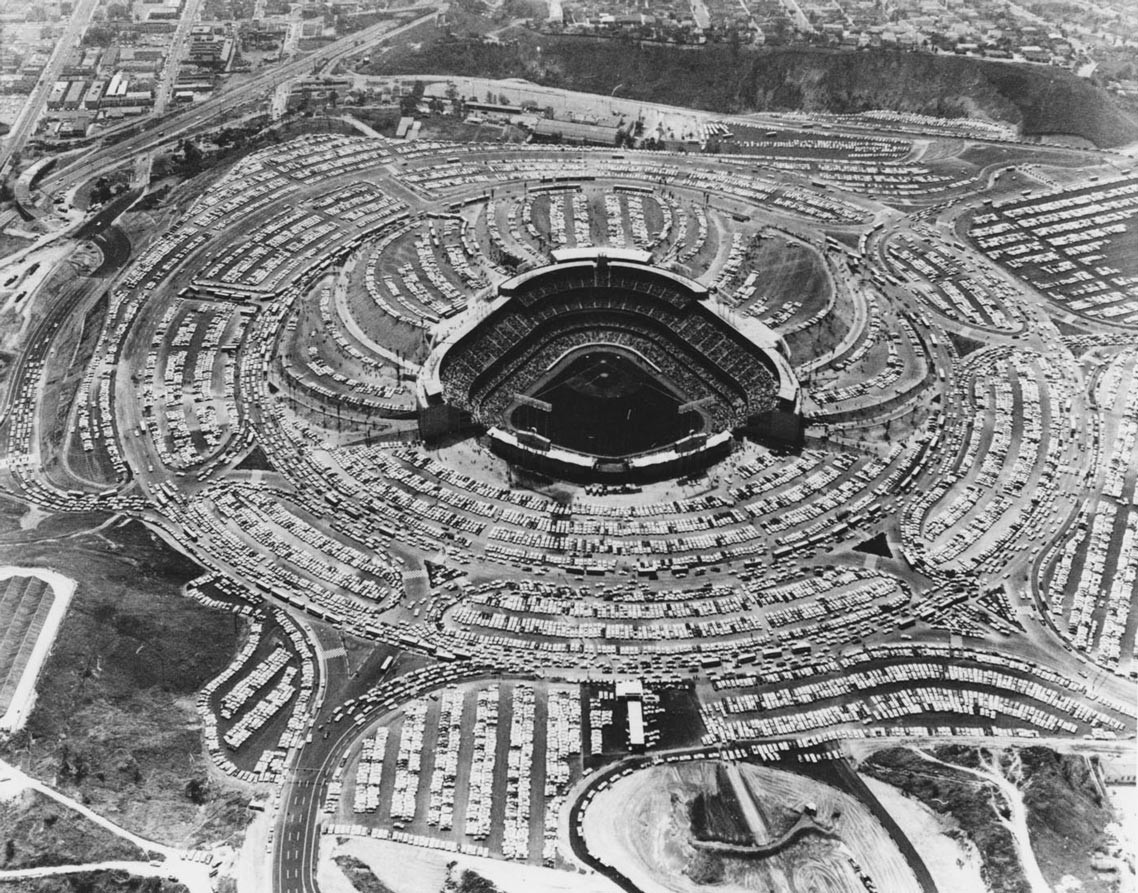
An aerial view of Opening Day 1962 with its record crowd of 52,564 as the Cincinnati Reds defeated the Dodgers, 6-3, on a three-run home run by veteran Wally Post.
AP Photo
Critically Acclaimed
The Reds’ leadoff batter, Eddie Kasko, christened the field with a double. He also scored the first run on a base hit by Vada Pinson. Snider delivered the Dodgers’ first hit and Jim Gilliam scored the first run. Ron Fairly doubled for the first Dodger RBI.
Although Los Angeles dropped the opener, 6-3, on a three-run home run by Cincinnati’s Wally Post, the energy and excitement associated with the Dodgers’ new ballpark was just beginning. Aerial photographers circled in helicopters for a better view of 52,564 patrons and a circular maze of automobiles with the downtown Los Angeles skyline in the background.
“All the minor problems were expected and conquered,” wrote The Times’ Hall. “The main thing is that the gates are open. Los Angeles has itself a major league ballpark, a truly remarkable stadium that is obviously destined to become recognized as the finest in the world. And those who were there will never forget how it all started on opening day.”
One of the biggest stories of the first week was a lack of drinking fountains, an oversight that gained national attention in cartoons and other press parodies. According to Dodger General Manager Buzzie Bavasi, the planners also forgot to install electrical outlets in the clubhouses. But the water issue was the most famous subject, even though every design aspect had to be approved by the City Council.
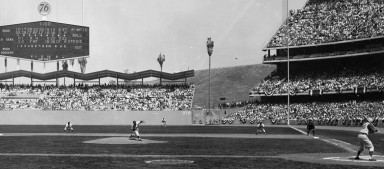
Left-hander Johnny Podres, the hero of the Brooklyn Dodgers’ World Series Championship in 1955, christens new Dodger Stadium with its first pitch on April 10, 1962.
As drinking fountains were installed, other oversights in baseball history were recalled. At the new Yankees’ spring training headquarters in Fort Lauderdale, the flag-raising ceremony was delayed when it was discovered the builder had forgotten to include a flag pole. There were no drinking fountains at L.A.’s Olympic Auditorium. At Brooklyn’s Ebbets Field, the construction of a press box was overlooked, as were women’s restrooms at the Yale Bowl Los Angeles Times, April 18, 1962 .
On April 12, representatives from the Yale and Towne Manufacturing Company presented O’Malley with a gold grand master key to the new Dodger Stadium. The new stadium was entirely equipped with Yale locks, all of which under a grand master key system. A similar gold grand master key was made and presented to the President of the United States upon the renovation of the White House. Vice Presidents Bavasi, Walsh and Fresco Thompson received silver master keys and Kay O’Malley received a gold bracelet because April 12 was her birthday.
The Dodgers were a hit on the field and at the box office, but O’Malley and his staff continued to analyze the new venue to better accommodate the comfort and overall experience of the fans.
On April 16, O’Malley wrote a 27-item checklist for Walsh to check on various aspects of the new ballpark. For example, the first item was a suggestion from umpire Al Barlick: “Foul line between home and first should be re-laid before starting of play.” Other subjects included dugout ushers, elevator signs, truck delivery schedules, bullpen locations, visiting clubs, playing field security, lost and found procedures, office luncheon meals and the problem of fans climbing up and down the exterior banks of the stadium.
Lasting Impressions
“At our staff meeting, we asked our organizational people to give you written memorandums of constructive ideas and pointing out problems that should be solved,” O’Malley wrote Walsh. “This is why I have dictated the above. It will be better to do it in writing than having the word going around by mouth to ear as we have a tremendous challenge before us to make this stadium function smoothly and we should all be striving to cooperate. Many of us have been working around the clock and it would be very easy to blow off steam, but let’s save that energy to keep the operation moving smoothly. Thanks a lot.”
As the finishing touches continued, so did the lavish praise from spectators making their first impression of what others were calling “baseball’s Taj Mahal.”
Noted Los Angeles Times columnist Jack Smith decided in the summer to check out the new ballpark. The Southern California native returned with a nostalgic account of his experience and his comments predicted lasting greatness for the stadium.
“It seems unique and marvelous to me because it couldn’t have happened in any other time in place in civilization, and it will most likely never happen again,” Smith wrote. “In 100 years, I predict, Dodger Stadium will be as great a curiosity as the Colossus of Rhodes and the Hanging Gardens of Babylon.
“This temple has been erected at the very zenith of the cult of Abner Doubleday, as the Parthenon was erected at the moment in history when the Greek spirit burned the brightest.”
In the June 20 edition of The Albuquerque Tribune, columnist Carlos Salazar summarized his first visit to Dodger Stadium with an observation about how fans in other baseball cities would expect to be treated if a new ballpark was constructed.
“O’Malley’s plant, in my opinion, is the baseball stadium of the future,” Salazar wrote. “You’re going to have to give John Q. Public something besides a hard-seat bench, a greasy hot dog and an ice-filled cup that passes as a soft drink. O’Malley went a bit further than most because his revolutionary plant offered many, many new items. He keeps you engrossed with the myriad of new offerings.”
When publicly reviewing the ballpark, O’Malley praised the overall use of color. “The white roof is extremely attractive,” he said. “I am pleased with the dimensions of the field. We aren’t getting any cheap home runs. I am crazy about the message board. I think our lighting is fine but some refocusing is required. There are too many lights focused on the stands and not enough on the field.” Sid Ziff, Los Angeles Times, 1962
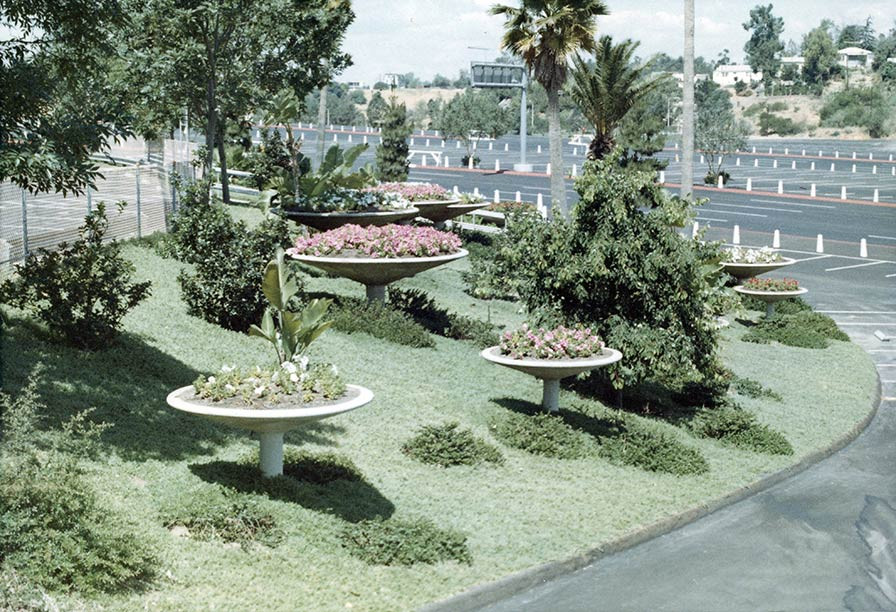
The colorful “champagne bowls” and greenery in the Dodger Stadium parking lots were a major part of the beautification project prior to the 1963 season.
Stadium Beautification Program
The 1962 Dodgers were exciting on the field as Tommy Davis won the first of two consecutive National League batting titles, and his 153 RBI remains a single-season franchise record. Drysdale won 25 games and the Cy Young Award while Wills stole a record 104 bases en route to Most Valuable Player honors.
The pennant race, though, caused problems for the Dodgers’ original practice of selling tokens instead of paper tickets for admission to the pavilions. Problems began when fans bought extra coins to insure against a future sold-out game, such as the San Francisco Giants series in mid-September, only to find early birds could buy coins on a particular day, leaving those with pre-purchased slugs on the outside. Another issue was the use of the stadium’s two elevators, which were never designed to accommodate 50,000 people. O’Malley promised a new parking plan to eliminate the reliance of elevators.
The Dodgers won 101 games during the regular season, but dropped a three-game playoff to San Francisco. The third and deciding game on October 3 provided the first Dodger Stadium heartbreak as the Giants rallied for four runs in the top of the ninth inning for a 6-4 victory.
Undaunted, O’Malley turned his sorrow to the soil. A $1.5 million beautification program, originally slated as a five-year project, was packed into one offseason. The bare hills in the back of the stadium were covered with the golden California poppy, along with a solid sea of blue and purple flowers. Palms and eucalyptus worth more than $104,000 were planted in the area fronting the ballpark. The hills in the background were laced with pipe for the sprinkler system. Poppy seed, containing its own fertilizer and hormones, was shot in with a gun.
To his season ticket customers, O’Malley sent a handkerchief with the Dodger logo and a promise: “We won’t blow it next year.” The Dodgers would win the World Series in 1963 with a four-game sweep of the New York Yankees, but an even bigger picture remained on O’Malley’s mind heading into the winter of 1962.
“Everything will be in bloom by June,” he predicted. “The setting will not be just beautiful, but dramatically beautiful so that people will come out raving.” Los Angeles Times, December 9, 1962
Mark Langill is team historian for the Los Angeles Dodgers. His 128-page book “Dodger Stadium” was released by Arcadia Publishing.